Refineries 101
We see them from the highway. We see them in the news. Oil refineries.
Sprawling, brightly lit engineering complexes. How do they work?
An oil refinery is basically a complex distillery where crude oil is boiled to separate a variety of chemical compounds.
1
The vapours rise in a distillation column—the tower in the refinery complex. Each hydrocarbon compound boils at a different temperature, referred to as a cut point. As the vapours cool, the liquids are isolated and drawn off.
2
The cracking process was developed to meet market demand by extracting more transportation fuels from a barrel of oil. Cat cracking uses a catalyst—a combination of alumina, silica and platinum—as well as heat and pressure to convert heavier oils into gasoline.
3
Hydrocracking uses hydrogen to increase the yield of higher value gasoline and produce other gasoline blending components.
4
The refining of crude oil leaves a residue of pitch or coke. A coker adds value by extracting usable product from this material. The coker is also used to refine oil sands bitumen.
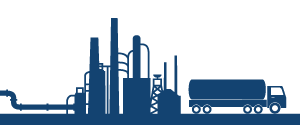
Small in comparison to other refineries internationally, Canada’s refineries must be extremely efficient to remain viable. They should be located close to crude oil sources or product markets to reduce transportation logistics.
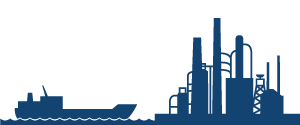
To export products globally, refineries must be built close to tidewater to take advantage of lower shipping costs. Refineries must also have ready access to affordable utilities such as electricity and natural gas to ensure efficient operation.
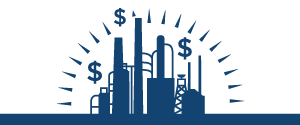
A new refinery would cost $15 billion or more. Other obstacles include regulatory issues, siting challenges and social license to operate. Refinery investments take 25 or 30 years to payout—a serious consideration when current demand for petroleum-based fuels is flat to declining.
Refining Process
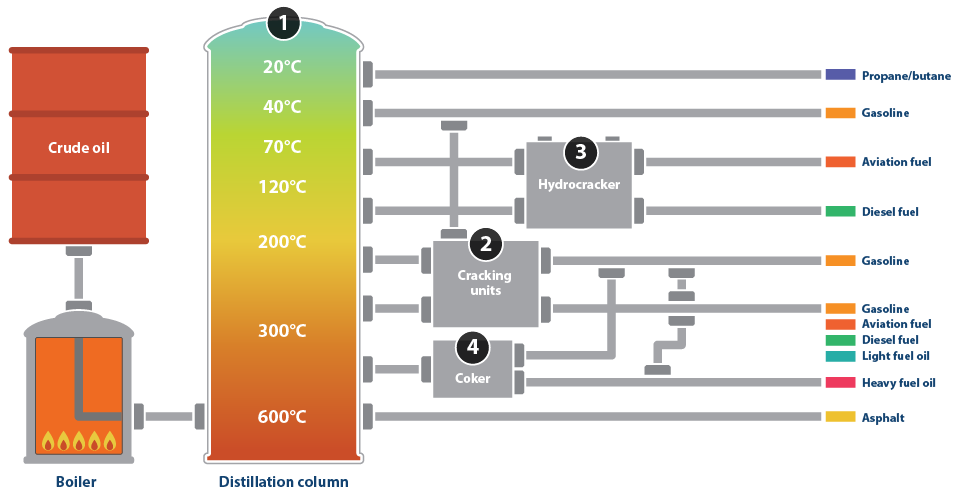
Average Output From A Barrel Of Oil (%), Canada
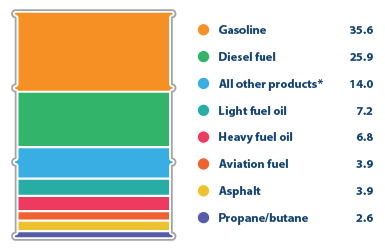